Contact Us To Get The Hot Product Catalog
We are constantly exploring products tailored for the structural steel pipe market.
Here, you will find a unique product line designed specifically for the global market that pursues excellence and quality, aimed at meeting your various needs. Our goal is to become a leading global manufacturer of structural steel pipes, providing every customer with the high-quality products and services they expect.
zinc aluminium magnesium coating steel pipe
Compared to traditional galvanized steel tubes, zinc aluminium magnesium coating steel pipes have significantly improved corrosion resistance and self-healing performance, helping to extend the service life of the bracket. The advantages of zinc aluminum magnesium steel tubes in photovoltaic brackets are very significant. Zinc-aluminium-magnesium steel tubing offers lighter weight with great corrosion resistance.
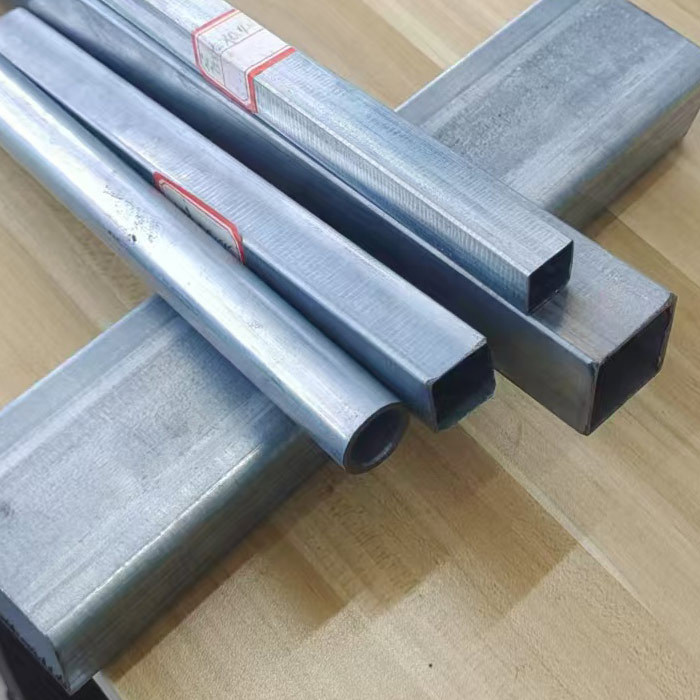
Zinc Aluminium Magnesium Coating Steel Pipes
Square:10*10*0.5mm-200*200*2.75mm
Rectangular:10*15*0.5mm-150*250*2.75mm
Round:φ10.3*0.5mm-200*3mm
Brand:Yuantai Derun or OEM
Grade:S350GD
Length: 0.5-24M or Cut as your need
MOQ: 2-5 Tons
Payment Term: TT/LC
Surface Treatment:Zinc aluminum magnesium alloy coating
Delivery time: 2-35 days
Capacity: 1 million tons/year
Port of shipment: Tianjin Xin Port
Advantages
At Yuantai Derun, zinc magnesium aluminum coating steel pipes have those advantages:
1. Corrosion Resistance
Adding alloy elements such as aluminum, magnesium, and silicon to the coating of zinc aluminum magnesium steel pipes greatly improves the corrosion inhibition effect, which is several times higher than that of ordinary pre galvanized steel pipes.
2. Self Repair
The coating components around the cutting surface continuously dissolve, forming a dense protective film, mainly composed of zinc hydroxide, alkaline zinc chloride, and magnesium hydroxide. This protective film has low conductivity and can inhibit corrosion on the cutting surface.
3. Longevity
Due to its strong corrosion resistance and self-healing effect on the cutting surface, components made of zinc, aluminum, magnesium, and other materials have a very long service life, typically reaching over 30 years.
4. Easy To Process
Compared with galvanized sheet, the coating of zinc aluminum magnesium steel plate is denser, so it is not easy to produce coated glass during the stamping process. It has excellent performance during welding processes such as stretching, stamping, bending, and harsh conditions, and has good resistance to damage due to the high hardness of the coating.
5. Good Scratch Resistance Of The Coating
The planar corrosion of ordinary galvanized steel pipes mostly occurs at scratches, which are an inevitable phenomenon of coated plates. After repeated experiments, it has been found that during the processing of zinc aluminum magnesium coated steel pipes, the surface coating itself has good scratch resistance, which can greatly avoid scratches.
6. Weldability
Compared to hot-rolled and cold-rolled pipes, the welding performance of ZAM(Zinc-aluminium-magnesium) steel pipe is slightly poor, but it can still be welded with reasonable processes and achieve the required strength, without affecting its use.
7. Lighter Weight
Zinc-aluminium-magnesium steel pipes provide lighter weight, an advantage that is reflected in photovoltaic mounts, some of which are roof-mounted, reducing the load-bearing weight of the roof of the house.
8. ZAM's Competitiveness And Irreplaceability
The following situations are the only ones where zinc aluminum magnesium can be used, and other products cannot be replaced:
(1) In outdoor long-term use situations, such as high-speed guardrails, product specifications are required to be thick and the surface coating is thick. Previously, batch galvanizing had to be used. However, after the birth of zinc aluminum magnesium, continuous hot dip galvanizing of aluminum magnesium can be used. Such products include solar equipment brackets, bridge components, and so on;
(2) In situations where salt is needed on roads in Europe and other regions, if other coatings are used to produce car soleplates, they will quickly corrode and must be manufactured using zinc aluminum magnesium plates. Such cases include buildings such as seaside villas;
(3) Special occasions that require acid resistance, such as poultry houses and food troughs on farms, where poultry manure is acidic, must use zinc aluminum magnesium boards that are more resistant to acid washing and corrosion.
Common Materials
S350GD ,S390GD,S420GD, S450GD,S550GD.
Zinc Aluminum Magnesium Coating(ZAM) Steel Pipes On Sale
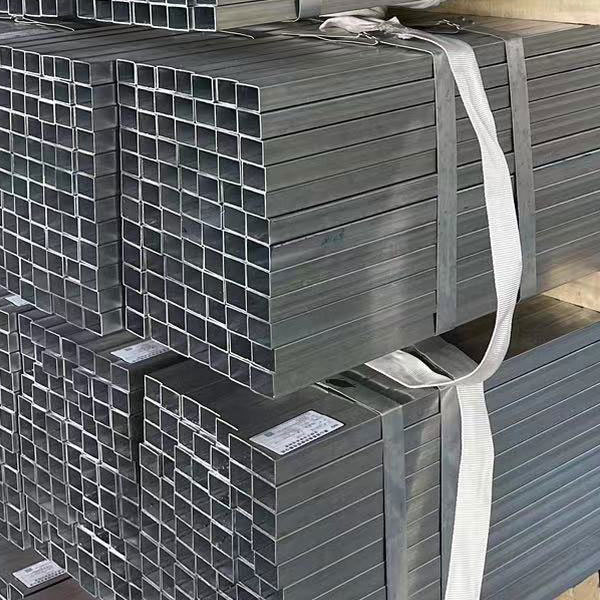
ZMA square steel tube
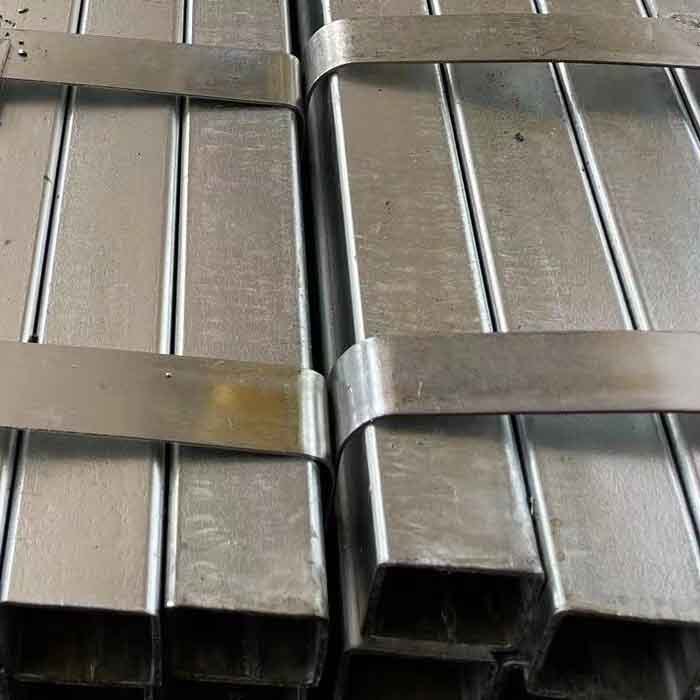
ZMA rectangular steel tube
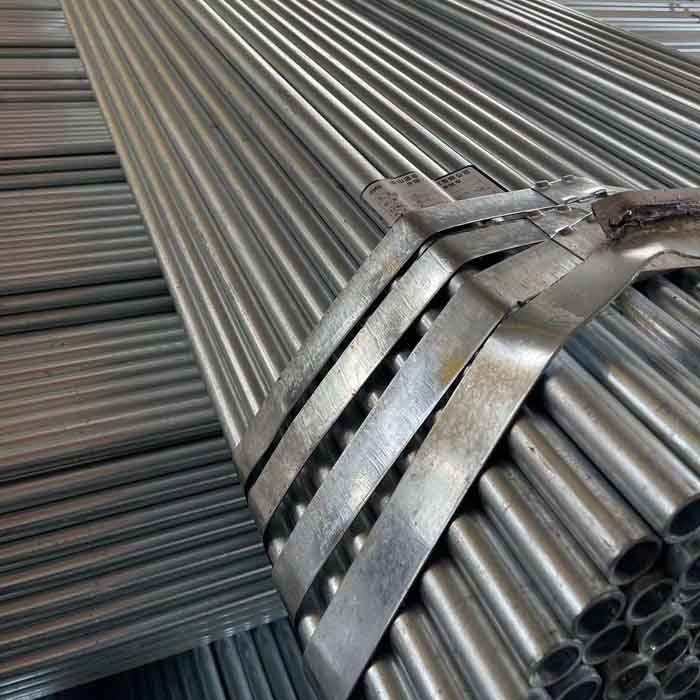
ZMA round steel pipe
Salt Spray Test
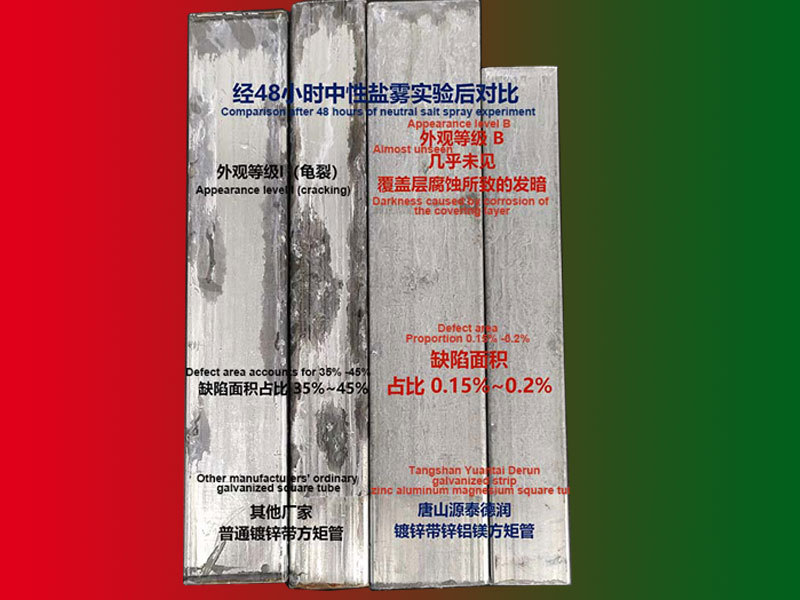
Through comparative tests, the new product of Tangshan Yuantai Derun Steel Pipe Co., Ltd., galvanized strip zinc aluminum magnesium square tube, has much better environmental corrosion resistance than ordinary galvanized strip square tube products.
Zinc aluminum magnesium has the ability to self repair the cut section of the coating. During use, the zinc aluminum magnesium material gradually forms a dense protective film (i.e. white rust) composed of zinc hydroxide, alkaline zinc chloride, and magnesium hydroxide near the cut or scratch location, which has good adhesion, high density, and low conductivity. It can effectively separate external corrosive media from the exposed metal substrate, thereby preventing further corrosion of the exposed cut, It has an inhibitory effect on corrosion in cut and scratch locations. At present, the cutting and surface neutral salt spray tests of zinc aluminum magnesium materials have reached 4440 hours without red rust.
Application
1.Construction industry
At present, in engineering projects, the floor bearing plate will directly contact with the concrete. The hardened concrete contains small gel like pores and large capillary holes, so water, air and other media may penetrate into the concrete. The water that accumulates in the concrete pores comes from soluble substances filtered out from the solid inside the cement, which is alkaline and has strong corrosion resistance throughout the entire application process. Therefore, zinc aluminum magnesium can be used in the construction industry. Currently, floor bearing plates in the construction industry are mainly galvanized with patterns.
2. Animal husbandry industry
With the vigorous development of the animal husbandry industry in recent years, the demand for breeding sheds is also increasing. At present, most enterprises use steel structure construction, and materials require high zinc layer hot dip galvanizing or aluminum zinc plating products in addition to infrastructure. The breeding environment in the animal husbandry industry is relatively unique, and there is a high demand for products. From previous applications, corrosion, paint peeling, bubbles, and other phenomena will occur soon. So zinc aluminum magnesium products have the characteristics of super corrosion resistance, self-healing, and easy processing, thus meeting the special needs of the livestock industry.
3. Photovoltaic bracket
The performance of zinc aluminum magnesium material is stable, and the material specifications and dimensions are easy to control, facilitating the standardization and mass production of photovoltaic brackets. Zinc aluminum magnesium materials have been used in the photovoltaic industry and have been recognized by many power companies due to their excellent surface quality, super corrosion resistance, stable performance, good environmental performance, and low-cost advantages. They have also brought good economic benefits to society.
Zinc Aluminum Magnesium Steel Pipe Sizes
Production process of zinc aluminum magnesium steel tubes
Step 1. Uncoiling and shear butt welding of inspected zinc-aluminum-magnesium coated steel coils.
Step 2. Straightening
Step 3. Roll Forming
Step 4. High Frequency Welding
Step 5. Weld Burr Removal
Step 6. Sizing
Step 7. Cutting
Step 8. Testing
Step 9. Packing
6 results
ViewShowcase
Top-Notch Zinc Aluminum Magnesium Coated Square Steel Tubes: Preferred by Leading Wholesalers, Distributors, and OEM Partners.
Zinc Aluminum Magnesium Coated Rectangular Steel Tubes manufacturer yuantaiderun, low cost,high quality,fast delivery.
Zinc Aluminium Magnesium Coating Perforated Square Tube,low cost,high quality,complete specifications,fast delivery.
Zinc Aluminum Magnesium Coated Steel Pipe For Photovoltaic Brackets. low cost,high quality,complete specifications,fast delivery.
Zinc Aluminium Magnesium Coating Round Steel Pipe wholesale yuantaiderun,low cost,high quality complete sizes,fast delivery.
Customized Zinc Aluminum Magnesium Coated Steel Tube,low cost,high quality,complete specifications,fast delivery.
Categories
- square steel pipe
- rectangular steel pipe
- round steel pipe
- shaped tube
- LSAW steel pipe
- zinc aluminium magnesium coating steel pipe
- galvanized steel pipe
- ERW steel pipe
- seamless steel pipe
- spiral steel pipe
- LINE PIPE&OCTG
- stainless steel pipe
- steel coil
- steel plate
- ship building steel pipe
- photovoltaic bracket
- steel profile
- Steel Pipe
- Steel Profile
- Steel Coil
- USE
- Structural steel pipe
- Fluid pipe
- Shape
- Square steel pipe
- Rectangular steel pipe
- Round steel pipe
- Shape tube
- Turface Treatment
- Black steel tube
- Pre galvanzied steel tube
- Hot dip galvanized steel tube
- Zinc aluminum magnesium coating steel tube
- Material
- Carbon steel pipe
- Alloy steel pipe
- Stainless steel pipe
- Standard
- EN10210
- EN10219
- ASTM A500
- ASTM A501
- ASTM A53
- ASTM A106
- ASTM A572
- ASTM A992
- JIS G3466
- AS/NZS 1163
- CSA G40.20
- CSA G40.21
- API 5L
- API 5CT
- Molding Process
- ERW steel pipe
- LSAW steel pipe
- Spiral welded steel pipe
- Seamless steel pipe
- Sales Attributes
- Sample list
- OEM
- ODM
- New arrival
- Basic style
- Star style
- Cross Section
- C channel
- Z channel
- U channel
- Round steel rod
- Rebar
- Angle steel
- H beam
- Raw material
- carbon steel profile
- Stainless steel profile
- Alloy steel profiles
- Surface Treatment
- Zinc aluminum magnesium steel coil
- GI steel coil
- PPGI coil
- Stainless steel coil
- Steel plate
- Steel strip
subscription
Please send your message to us
Yuantai team has over 21 years of experience in steel pipe project applications, specializing in the production, manufacturing, and customization of square rectangular, and circular steel pipes. Warmly welcome project procurement managers, individual owners, designers, and overall sellers, etc. Write down your requirements and receive professional quotes and technical support.
- Name
- Tel
- *Title
- *Content