-
Categories
-
Steel Pipe
-
Steel Profile
-
Steel Coil
-
USE
Structural steel pipe Fluid pipeShape
Square steel pipe Rectangular steel pipe Round steel pipe Shape tubeStandard
EN10210 EN10219 ASTM A500 ASTM A501 ASTM A53 ASTM A106 ASTM A572 ASTM A992 JIS G3466 AS/NZS 1163 CSA G40.20 CSA G40.21 API 5L API 5CTMaterial
Carbon steel pipe Alloy steel pipe Stainless steel pipeMolding Process
ERW steel pipe LSAW steel pipe Spiral welded steel pipe Seamless steel pipeTurface Treatment
Black steel tube Pre galvanzied steel tube Hot dip galvanized steel tube Zinc aluminum magnesium coating steel tubeSales Attributes
Sample list OEM ODM New arrival Basic style Star style -
-
Home / Heat Treatment
Heat Treatment
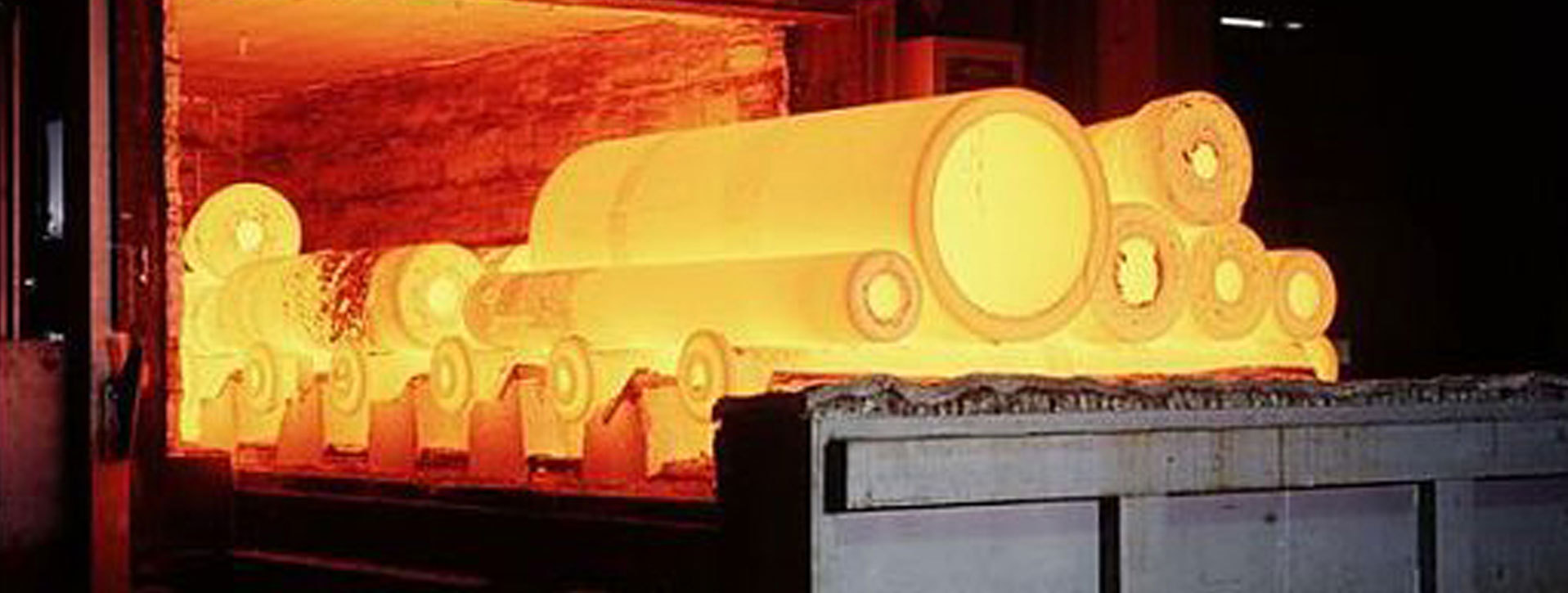
Yuantai Derun Steel Pipe Manufacturing Group has numerous heat treatment processes for steel pipes and steel pipe fittings, which are generally related to the usage scenarios of customer pipes. Different structural pipe fittings for different purposes use different heat treatment methods. The following are common heat treatment methods.
1. Annealing
Operation method: Heat the steel parts to a temperature of Ac3+30-50 degrees or Ac1+30-50 degrees or below (relevant information can be consulted), and generally cool slowly with the furnace temperature.
Purpose: 1. Reduce hardness, improve plasticity, and improve cutting and pressure processing performance; 2. Refine grain size, improve mechanical properties, and prepare for the next process; 3. Eliminate the internal stress caused by cold and Hot working.
2. Normalization
Operation method: Heat the steel parts to 30~50 degrees above Ac3 or Accm, keep them warm, and then cool them at a slightly faster cooling rate than annealing.
Purpose: 1. Reduce hardness, improve plasticity, and improve cutting and pressure processing performance; 2. Refine grain size, improve mechanical properties, and prepare for the next process; 3. Eliminate the internal stress caused by cold and Hot working.
3. Quenching
Operation method: Heat the steel piece to a phase change temperature of Ac3 or Ac1 or above, keep it warm for a period of time, and then quickly cool it in water, nitrate, oil, or air.
Purpose: Generally, quenching is to obtain high hardness Martensite structure. Sometimes, when quenching some high alloy steels (such as stainless steel and wear-resistant steel), it is to obtain a single and uniform austenite structure to improve wear resistance and corrosion resistance.
Application points: 1. Generally used for carbon steel and alloy steel with a carbon content greater than 0.3%; 2. Quenching can fully utilize the strength and wear resistance potential of steel, but it can also cause significant internal stress, reducing the plasticity and impact toughness of the steel. Therefore, tempering is necessary to obtain better comprehensive mechanical properties.
Purpose: Generally, quenching is to obtain high hardness Martensite structure. Sometimes, when quenching some high alloy steels (such as stainless steel and wear-resistant steel), it is to obtain a single and uniform austenite structure to improve wear resistance and corrosion resistance.
Application points: 1. Generally used for carbon steel and alloy steel with a carbon content greater than 0.3%; 2. Quenching can fully utilize the strength and wear resistance potential of steel, but it can also cause significant internal stress, reducing the plasticity and impact toughness of the steel. Therefore, tempering is necessary to obtain better comprehensive mechanical properties.
4. Tempering
Operation method: Reheat the quenched steel parts to a temperature below Ac1, and after insulation, cool them in air or oil, hot water, or water.
Purpose: 1. Reduce or eliminate internal stress after quenching, reduce deformation and cracking of the workpiece; 2. Adjust the hardness, improve plasticity and toughness, and obtain the mechanical properties required for work; 3. Stabilize the workpiece size.
5. Conditioning
Operation method: High temperature tempering after quenching is called quenching and tempering, which means heating the steel piece to a temperature 10-20 degrees higher than the quenching temperature, holding it for quenching, and then tempering at a temperature of 400-720 degrees.
Purpose: 1. Improve cutting performance and improve the smoothness of the machining surface; 2. Reduce deformation and cracking during quenching; 3. Obtain good comprehensive mechanical properties.
6.Limitation
Operation method: Heat the steel parts to 80-200 degrees Celsius, keep them warm for 5-20 hours or more, and then take them out with the furnace and cool them in air.
Purpose: 1. To stabilize the microstructure of quenched steel parts and reduce deformation during storage or use; 2. Reduce internal stress after quenching and grinding, stabilize shape and size.
7. Cold Treatment
Operation method: Cool the quenched steel parts in a low-temperature medium (such as dry ice or liquid nitrogen) to -60~-80 degrees Celsius or lower, and remove them to room temperature after the temperature is uniform.
Purpose:
1. Make all or most of the residual austenite in the quenched steel parts convert to Martensite, so as to improve the hardness, strength, wear resistance and Fatigue limit of the steel parts;
2. Stabilize the structure of steel to stabilize the shape and size of steel components.
Application points:
1. After quenching, steel parts should be immediately subjected to cold treatment, followed by low-temperature tempering to eliminate internal stress during low-temperature cooling;
2. Cold treatment is mainly applicable to tight cutting tools, measuring tools, and tight parts made of alloy steel.
Purpose:
1. Make all or most of the residual austenite in the quenched steel parts convert to Martensite, so as to improve the hardness, strength, wear resistance and Fatigue limit of the steel parts;
2. Stabilize the structure of steel to stabilize the shape and size of steel components.
Application points:
1. After quenching, steel parts should be immediately subjected to cold treatment, followed by low-temperature tempering to eliminate internal stress during low-temperature cooling;
2. Cold treatment is mainly applicable to tight cutting tools, measuring tools, and tight parts made of alloy steel.
8. Flame Heated Surface Quenching
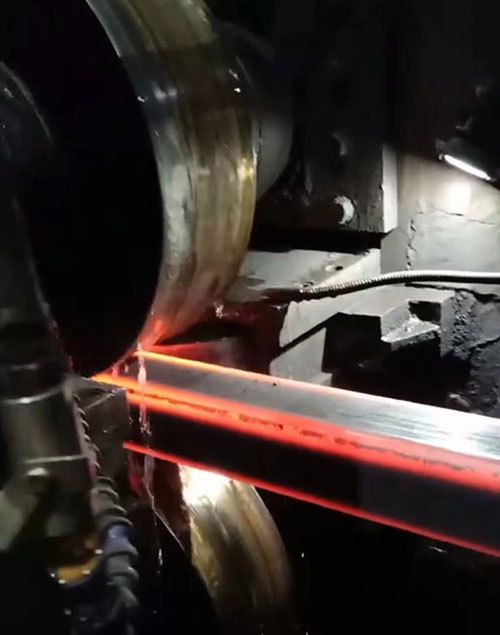
Quadrangle heating
To address the defects in the corners of traditional cold-formed square steel pipes, this utility model proposes a square rectangular steel pipe formed by thickening the corners and combining cold and hot forming. Introducing hot forming technology, namely local induction heating technology, into traditional roll bending forming processes. High temperature can not only reduce the forming force of materials, but also improve their formability; And it can eliminate residual stress and possible cracking caused by work hardening. At the same time, the corner contour of the square steel pipe formed by cold and hot composite forming is dense, with a small inner and outer corner radius, and the corner angle is close to 90 °, accompanied by corner thickening.
Operation method: Use a flame of oxygen acetylene mixture gas to burn, spray it onto the surface of the steel piece, quickly heat it, and immediately spray water for cooling when the quenching temperature is reached.
Purpose: To improve the surface hardness, wear resistance, and fatigue strength of steel parts, while maintaining a ductile state in the heart.
Application points:
1. It is commonly used for medium carbon steel parts, and the depth of the quenching layer is generally 2-6mm;
2. Suitable for large workpieces produced in single or small batches and workpieces that require local quenching.
Purpose: To improve the surface hardness, wear resistance, and fatigue strength of steel parts, while maintaining a ductile state in the heart.
Application points:
1. It is commonly used for medium carbon steel parts, and the depth of the quenching layer is generally 2-6mm;
2. Suitable for large workpieces produced in single or small batches and workpieces that require local quenching.

9. Induction Heating Surface Quenching
Operation method: put the steel part into the inductor, make the surface of the steel part produce induced current, heat it to the quenching temperature in a very short time, and then spray water for cooling.
Purpose: To improve the surface hardness, wear resistance, and fatigue strength of steel parts, while maintaining a ductile state in the heart.
Application points:
1. Mainly used for medium carbon steel and alloy structural steel parts in the nave;
2. Due to the skin effect, the quenching layer of high-frequency induction quenching is generally 1-2mm, the medium frequency quenching is generally 3-5mm, and the high-frequency quenching is generally greater than 10mm
Purpose: To improve the surface hardness, wear resistance, and fatigue strength of steel parts, while maintaining a ductile state in the heart.
Application points:
1. Mainly used for medium carbon steel and alloy structural steel parts in the nave;
2. Due to the skin effect, the quenching layer of high-frequency induction quenching is generally 1-2mm, the medium frequency quenching is generally 3-5mm, and the high-frequency quenching is generally greater than 10mm
10. Carburization
Operation method: Place the steel part in a carburizing medium, heat it to 900~950 degrees, and keep it insulated to obtain a certain concentration and depth of carburizing layer on the surface of the steel part.
Purpose: To improve the surface hardness, wear resistance, and fatigue strength of steel parts, while maintaining a ductile state in the heart.
Application points:
1. Used for low-carbon steel and low alloy steel parts with a carbon content of 0.15% to 0.25%, generally with a carburized layer depth of 0.5 to 2.5mm;
2. After carburizing, quenching must be carried out to make the surface obtain Martensite, so as to achieve the purpose of carburizing.
Purpose: To improve the surface hardness, wear resistance, and fatigue strength of steel parts, while maintaining a ductile state in the heart.
Application points:
1. Used for low-carbon steel and low alloy steel parts with a carbon content of 0.15% to 0.25%, generally with a carburized layer depth of 0.5 to 2.5mm;
2. After carburizing, quenching must be carried out to make the surface obtain Martensite, so as to achieve the purpose of carburizing.
11. Nitridation
Operation method: Utilize the active nitrogen atoms decomposed from ammonia gas at 5. -600 degrees Celsius to saturate the surface of the steel piece with nitrogen, forming a nitride layer.
Purpose: To improve the surface hardness, wear resistance, fatigue strength, and corrosion resistance of steel parts.
Application points: It is mainly used for medium carbon alloy structural steel containing aluminum, chromium, molybdenum and other alloy elements, as well as carbon steel and cast iron. The depth of the nitriding layer is generally 0.025-0.8mm
Purpose: To improve the surface hardness, wear resistance, fatigue strength, and corrosion resistance of steel parts.
Application points: It is mainly used for medium carbon alloy structural steel containing aluminum, chromium, molybdenum and other alloy elements, as well as carbon steel and cast iron. The depth of the nitriding layer is generally 0.025-0.8mm
12. Nitrocarburizing
Operation method: Simultaneously carburize and nitride the surface of the steel component.
Purpose: To improve the surface hardness, wear resistance, fatigue strength, and corrosion resistance of steel parts.
Application points:
1. It is mainly used for low carbon steel, low alloy structural steel and Tool steel products, and the nitriding layer is generally 0.02~3mm deep;
2. After nitriding, quenching and low-temperature tempering are also required.
Purpose: To improve the surface hardness, wear resistance, fatigue strength, and corrosion resistance of steel parts.
Application points:
1. It is mainly used for low carbon steel, low alloy structural steel and Tool steel products, and the nitriding layer is generally 0.02~3mm deep;
2. After nitriding, quenching and low-temperature tempering are also required.
Product
- Square Steel Pipe
- Rectangular Steel Pipe
- Round Steel Pipe
- Special Shaped Steel pipe
- LSAW Steel Pipe
- Zinc aluminium magnesium coating steel pipe
- Galvanized Steel Pipe
- ERW steel pipe
- Seamless steel pipe
- Spiral steel pipe
- LINE PIPE OCTG
- Ship Building Steel Pipe
- Stainless steel pipe
- Steel coil
- C channel
- Z channel
- Photovoltaic bracket
Reach us for
Please send your message to us
Yuantai team has over 21 years of experience in steel pipe project applications, specializing in the production, manufacturing, and customization of square rectangular, and circular steel pipes. Warmly welcome project procurement managers, individual owners, designers, and overall sellers, etc. Write down your requirements and receive professional quotes and technical support.
- Name
- Tel
- *Title
- *Content
- Upload
- Only supports .rar/.zip/.jpg/.png/.gif/.doc/.xls/.pdf, maximum 20MB.
- Address
Copyright © 2025 TIANJIN YUANTAI DERUN STEEL PIPE MANUFACTURING GROUP CO., LTD. Support By BEE Cloud